The redesigned seat could also save airlines $200 million.
The airline industry is undergoing drastic change, heralded both by the economy and new advancements in technology. And with very small profit margins, airlines are always looking for ways to save money.
One way to do that is to make airplanes lighter, which can be a serious saver of fuel costs across a fleet over time–for instance, one journalist calculated that just carrying one fewer bags of peanuts on flights for a year would save an airline $2,000 in fuel costs. Airlines have been known to powerwash their engines to remove dirt in order to save money. But shaving off weight savings is difficult when you can’t compromise on the highly regulated technical components of an aircraft, or control the weight of your passengers or their luggage. Instead, aerospace engineers look for marginal gains they can make in other areas of the plane, including the design of the interiors and the seats.
A super-light airplane seat frame, designed by a researcher at Autodesk, could be a valuable tool in that perennial quest to lighten an airplane’s load. Because of its computer-optimized, lattice-like structure–cast in magnesium, which is 35% lighter than the aluminum that’s conventionally used–the experimental seat frame is 56% lighter than what you’d typically find on an airplane.
That might not seem like a huge change, but over one year of flight for an A380 aircraft, it could amount to over $100,000 in savings. And over the 20-year lifetime of a fleet of 100 A380s? It could mean $200 million worth of savings. More importantly, that’s a reduction of nearly 140,000 tons of carbon in the atmosphere.
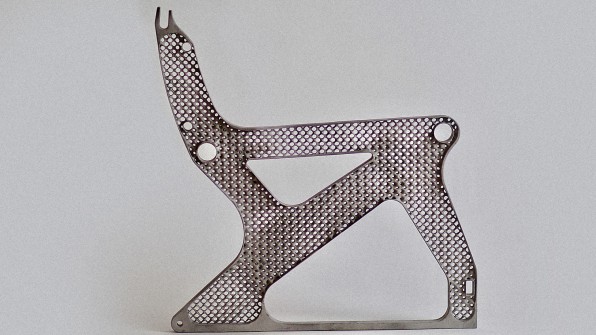
The lattice structure of the seat frame was conceived by Andy Harris, a design consultant in Autodesk’s Digital Manufacturing Group, as a proof of concept to show what the company’s technology could do. Made using Autodesk’s generative design software, which uses algorithms to find the optimal structure based on a set of parameters, the seat frame’s body is just as strong as its average counterpart, but 30% lighter.But while the organic-looking latticework created a lighter seat frame in theory, Harris hit a road block when it came to how to manufacture it. Generative design is often brought to life using 3D printing, because conventional casting methods can’t handle intricate designs. But Harris’s seat was unfeasible for 3D printing, because of the constraints of current commercial metal 3D printers, which are limited to a relatively small portfolio of materials—and using custom materials is costly.
Meanwhile, independently from Harris, another Autodesk researcher named Andreas Bastian, who specializes in 3D printing, came up with an entirely new manufacturing process that would combine the strengths of 3D printing with the strengths of traditional metal casting (which has been around since the Bronze Age approximately 5,000 years ago). Metal casting relies on a mold, often made of wax, sand, or some other burnable polymer, that is used to cast the desired object before being melted off. Unlike metal 3D printers, which are mostly restricted to items smaller than a breadbox, metal casting is used to make giant, 100,000-ton metal parts for things like jet engines. And it’s far less expensive.
Bastian combined the two methods, using a non-metal 3D printer as the mechanism for creating the mold rather than the thing itself. The 3D printer printed a pattern, which enables the manufacturers to create a negative mold using a material like ceramic. Objects could be cast in metal using the negative of the printed pattern. He realized his hybrid method could produce products that were once unfeasible—like Harris’s generative airplane seat frame.
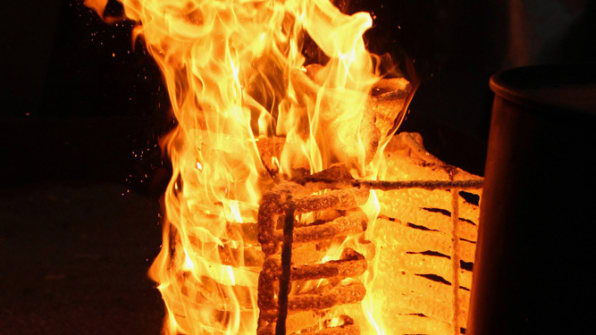
The two partnered up, and Bastian discovered a foundry in Michigan called Aristo Cast that would be able to fabricate a proof-of-concept airplane seat. An added bonus? Aristo Cast was comfortable working with magnesium—something no commercially available metal 3D printers were able to do. The material only recently passed a fire test, which is required by the Federal Aviation Administration, and was approved in 2015 for use on airplanes, though Autodesk says that it is unaware of any aircraft using a magnesium seat frame.Using magnesium reduced the design’s weight by another 24%, and the finished prototype for Autodesk’s super-light frame only weighs 1.69 pounds (a typical frame weighs 3.69 pounds). Such a dramatic change in weight was only possible by combining traditional metal casting with contemporary 3D printing.

Part of the strength of generative design is that it can be used to optimize materials for things like weight–as with Harris’s super-light seat frame–as well as temperature and aerodynamics. Now, combined with Bastian’s new manufacturing process, generative design could be used for a much wider array of parts and products than previously feasible. And Bastian says that since it’s highly likely that it will remain cheaper and faster to 3D print with polymers or sand than it is to print with metal over the next 10 to 20 years, his manufacturing method will enable generatively designed parts to be cast relatively cheaply.“We’re currently not asking very much of the things we’re designing in terms of function,” Bastian says. “We’re generally asking the part to hold the load and that’s it. But what’s exciting is we can start to ask a whole lot more of the materials around us and make them perform in more ways than one.”
Bastian and Harris are in talks with several airlines and aircraft manufacturers that are interested in exploring what’s possible using this combination of technologies. And while the super-light frame remains a proof of concept for now, it’s already winning awards; in 2017, it received the “Casting of the Year” award from the American Foundry Society.
The question remains–will a significantly lighter seat frame mean that airplanes can afford to splurge a little bit on leg room?
–
Featured Image: courtesy Autodesk
This article first appeared in www.fastcodesign.com
Seeking to build and grow your brand using the force of consumer insight, strategic foresight, creative disruption and technology prowess? Talk to us at +9714 3867728 or mail: info@groupisd.com or visit www.groupisd.com